An interconnected photoelectric smoke sensor is a life saving appliance that is designed to alert occupants of a fire and give them time to evacuate safely, and as such, it is a crucial component of QLD home safety. But have you ever wondered how a photoelectric smoke alarm is manufactured to to meet the highest standards of quality and safety? Manufacturers of a photoelectric smoke sensor must ensure their products are safe, reliable, and effective – this is where an ISO 9001 Quality Management System comes into play!
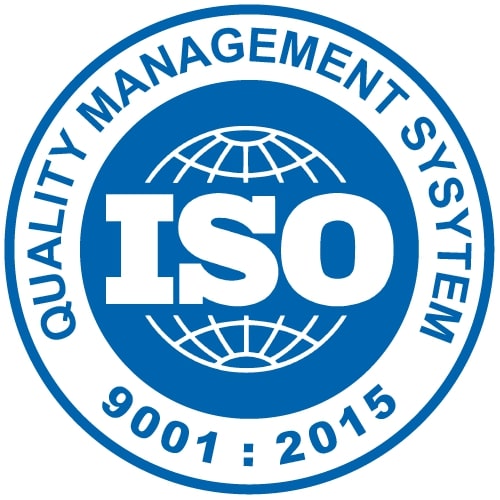
What is an ISO 9001 Quality Management System? (QMS)
ISO 9001 is a globally recognized standard for quality management systems. It provides a framework for organizations to establish and maintain systems that ensure consistent product quality. ISO 9001 is an important indicator of a company’s commitment to quality and customer satisfaction – it covers all aspects of an organization’s operations, including design, development, production, delivery, and support. Has your interconnected photoelectric smoke alarm come from an ISO 9001 accredited facility? (our ZEN Smoke Alarms do!).
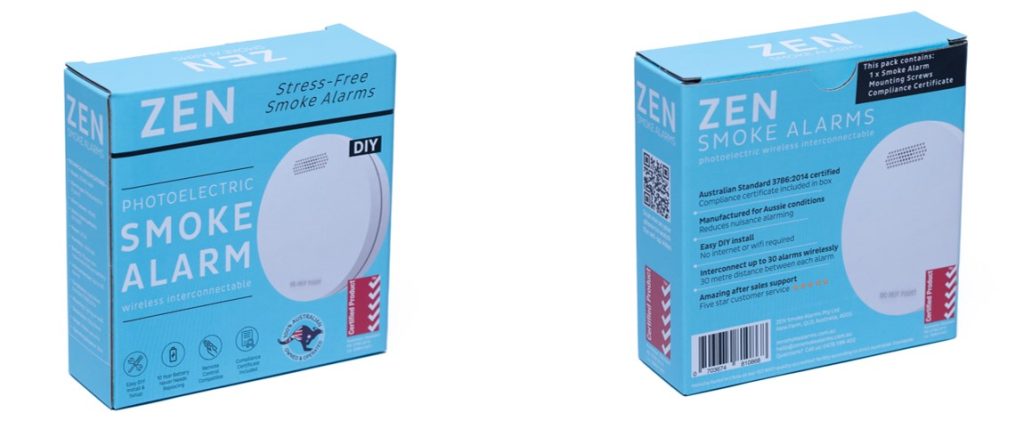
Photoelectric Smoke Sensors and ISO 9001 Quality
The commercial production of interconnected photoelectric smoke alarms involves sourcing high-quality materials, assembling the components, and then testing the finished product for quality and safety. ISO 9001 requires manufacturers to establish and document clear processes for sourcing these materials and assembling the product, as well as procedures for testing and inspecting the final product.
This includes strict supplier evaluations to ensure raw materials meet industry standards, precision manufacturing to guarantee consistency, and extensive quality control checks at multiple production stages. Additionally, ongoing audits and continuous improvement initiatives help maintain high safety and reliability standards, ensuring compliance with Australian Standard 3786:2014.
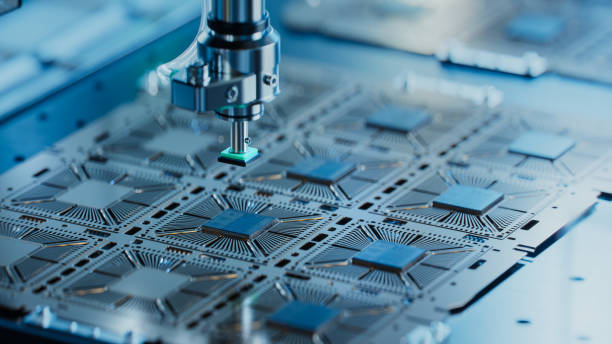
Testing is a key part of the manufacturing process for photoelectric smoke sensors. ISO 9001 requires manufacturers to establish rigorous testing procedures to ensure that every device meets the required safety standard (Australian Standard 3786:2014). This includes testing for sensitivity to smoke, false alarms, and battery life.
Additionally, environmental testing is conducted to assess performance under different conditions such as humidity, temperature fluctuations, and air pressure. Long-term durability tests ensure that alarms function reliably over their 10-year lifespan. By adhering to these strict protocols, manufacturers guarantee that the photoelectric smoke sensor provides accurate, consistent, and dependable fire detection for maximum safety.
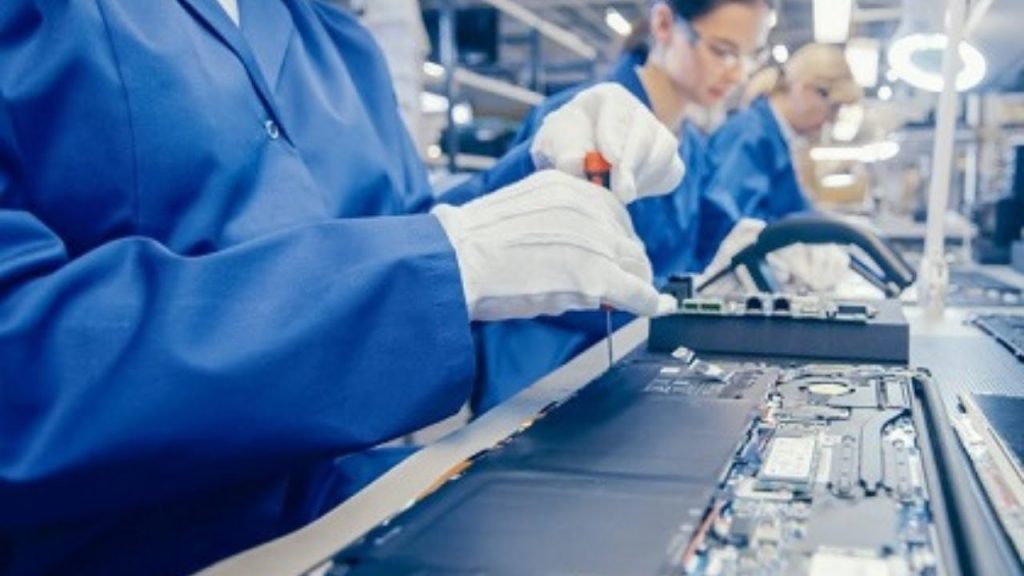
ISO 9001 Accreditation & Photoelectric Smoke Sensors
ISO 9001 certification also requires manufacturers to continuously monitor and improve their processes to ensure consistent product quality. This involves regularly reviewing and analyzing data to identify areas for improvement, and implementing changes to optimize the manufacturing process.
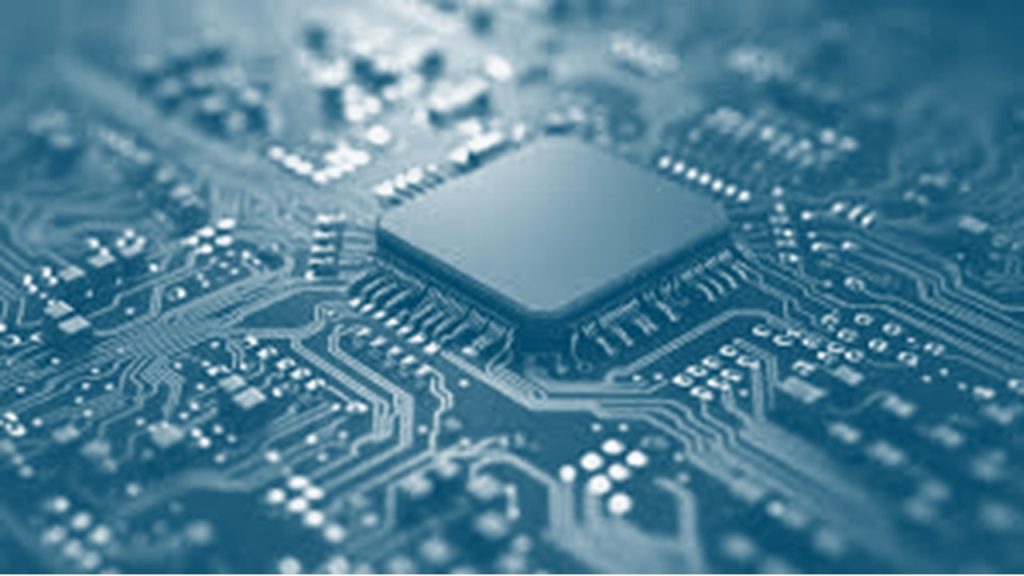
Manufacturers must also have processes in place to ensure that the photoelectric smoke sensor is delivered to customers safely and effectively. This means that the smoke alarms are packaged correctly and that they arrive at their destination without damage. Manufacturers must also ensure that customers can install and use the interconnected photoelectric smoke alarm correctly.
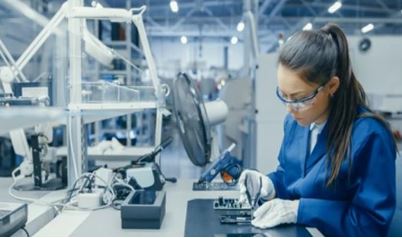
ISO 9001 Photoelectric Smoke Alarm Summary
Manufacturing interconnected photoelectric smoke alarms is a complex process that requires precision, attention to detail, and a commitment to quality and safety. ISO 9001 accreditation plays a crucial role in ensuring that every step of the process is documented, monitored, and continuously improved to meet the highest standards of quality and safety. By choosing a photoelectric smoke alarm manufacturer that is ISO 9001 accredited, you can have confidence that the interconnected photoelectric smoke alarms in your home are of the highest quality and will provide reliable protection for years to come.
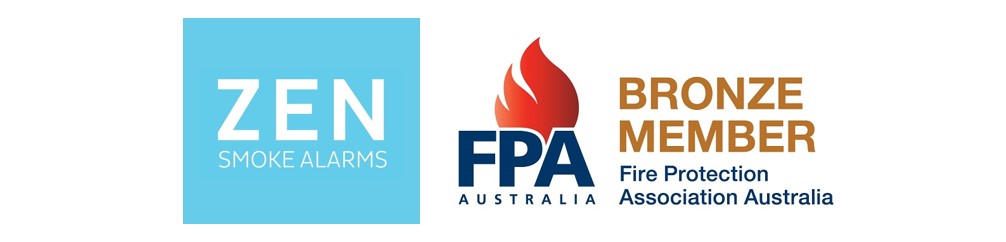
Want to know more? Watch our ZEN Smoke Alarm YouTube channel or call us on 0478 596 402 today
We love talking smoke alarms!
ZEN Photoelectric Smoke Alarms
New Farm, QLD, 4005